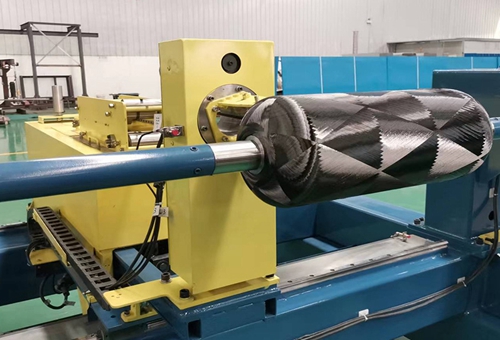
Composite Hydrogen Storage Cylinder Production Line
Filament winding is a manufacturing process used in the production of composite materials, including hydrogen cylinders, which are often made from lightweight, high-strength composite materials to store and transport hydrogen gas safely.
Here's an explanation of how a filament winding machine is used in the production of hydrogen cylinders:
Materials Selection: The process begins with the selection of suitable materials. In the case of hydrogen cylinders, the materials are typically composite materials, which can include carbon fiber, fiberglass, and epoxy resins. These materials are chosen for their high strength-to-weight ratio and resistance to corrosion.
Mandrel Preparation: A mandrel is a cylindrical tool or mold around which the composite materials will be wound. It is designed to the specific dimensions of the hydrogen cylinder. The mandrel is usually made of metal, and it needs to be thoroughly cleaned and coated with a release agent to prevent the composite material from sticking to it.
Winding Setup: The filament winding machine is set up with the appropriate program and parameters. These parameters include the angle at which the fibers are wound, the tension applied to the fibers, and the speed of the winding. These settings are critical in ensuring that the composite material is applied uniformly and that the resulting cylinder meets the desired specifications.
Winding Process: The composite material, typically in the form of rovings (bundles of fibers), is pulled through a resin bath to impregnate the fibers with epoxy resin. The resin-coated fibers are then wound onto the rotating mandrel. The filament winding machine precisely controls the winding pattern, ensuring that the composite material is layered at the specified angles and thicknesses. This controlled winding process is crucial for achieving the desired mechanical properties of the cylinder.
Curing and Consolidation: After the winding is complete, the hydrogen cylinder is still in its raw state and needs to be cured. The epoxy resin is heat-cured, which hardens the composite material. The curing process can take place in an oven or autoclave, depending on the materials and design requirements.
Post-processing: Once the curing process is complete, additional finishing and inspection steps are taken. This may include trimming excess material, inspecting for any defects, and adding additional features like valves and fittings.
Quality Control: Before the hydrogen cylinder is ready for use, it undergoes rigorous quality control and testing to ensure that it meets safety standards and performance requirements. This can include pressure testing, visual inspections, and other non-destructive testing methods.
Filament winding machines are highly precise and automated, making them well-suited for producing high-quality, lightweight, and strong composite hydrogen cylinders. The use of composite materials allows for a significant reduction in the weight of the cylinder while maintaining the necessary strength and safety for storing and transporting hydrogen gas.