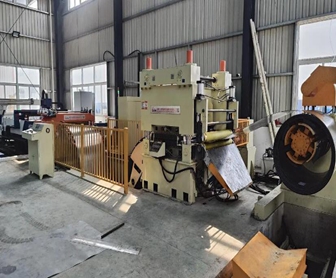
The Large-Scale LPG Cylinder Swing Feeding Automatic Discs Blanking Production Line is a specialized machine for disc feeding processing, especially suitable for stamping and forging processes with different material thicknesses and feeding step distances. Its main features include high feeding accuracy, high production efficiency, and cost savings. In addition, the skewed feeding machine can improve material utilization rate, reduce waste of corner materials, and thus lower production costs through the design of left-right skewed displacement. The working principle of the skewed feeding machine for liquefied gas cylinders is to place the coil material on a heavy-duty material rack, unwind it, and feed it into the leveling machine. The leveled material then enters the feeding machine. The feeder controls the distance and speed of material advancement through the material forward conveying device, while controlling the distance of material lateral translation through the lateral translation driving device. In this way, when the first stamping is completed on the steel plate strip, the CNC device of the skewed feeding machine will drive the movable frame to move horizontally, thereby achieving the stamping and material dropping of the circular plate.At present, the large-scale LPG cylinder wwing feeding automatic discs blanking production line has gradually replaced the traditional hydraulic press series disc machines.
The swing feeding machine controls the stamping action of the stamping continuous die through a servo motor, and controls the lateral translation distance of the material through a lateral translation drive device, so that the stamping continuous die stamps the sheet metal one by one along the lateral arrangement direction. The swing feeder is easy to operate and has a high degree of automation. In the production of liquefied gas cylinders, it can achieve fully automated operation. In the continuous stamping process, the feeding error can be controlled within plus or minus 0.08mm, greatly reducing the waste of corner materials generated by stamping discs, reducing production processes, saving time and effort, reducing production costs, and greatly improving production efficiency. The skewed feeding machine is suitable for large-scale stamping production of various specifications of circular discs, with a wide range of applications and the ability to handle materials with a width of up to 1600mm and a diameter of up to 800mm.
Equipments,Machines & Sytem:
No. |
Description |
Quantity (Set) |
1 |
Hydraulic Feeding Trolley |
1 |
2 |
Hydraulic Single Head Cantilever Unwinding Machine |
1 |
3 |
Hydraulic Cantilever Supportor |
1 |
4 |
Hydraulic Telescopic Plate Holding Tool |
1 |
5 |
Precision Plate Leveling Machine |
1 |
6 |
Material Pit Transition Bridge |
1 |
7 |
Anti-Scratch Bracket for Material Pit |
1 |
8 |
Material Pit Guardrail |
1 |
9 |
Side Guide Position Width Adjustment Device |
1 |
10 |
Left-Right Displacement Leveling Servo Feeder |
1 |
11 |
High Performance Gantry Press Machine |
1 |
12 |
Conveyor |
1 |
13 |
Palletizing Device for Circular Discs |
1 |
14 |
Shear Wasting Plate Machine |
1 |
15 |
Hydraulic System |
1 |
16 |
Electronic Control System |
1 |
(1)Applicable Steel Coil Specifications:
Applicable materials: National standard genuine materials
Cold-rolled sheet/pickled sheet/hot-rolled sheet/galvanized sheet and other metal coils
Material thickness: 1.0mm to 4.5mm
Material width: 1250mm (minimum 200mm)
Steel coil inner diameter:Φ 480mm - Φ 530mm - Φ 610mm
Outer diameter of steel coil:Φ 1500mm
Steel coil weight: ≤ 20 tons
(2)Equipment Parameters:
Feeding length: 50mm-1000mm
Feeding tolerance: 200mm ± 0.3mm
Deviation tolerance: L=200mm ± 0.6mm
Blanking speed: Φ 300 ≤ 35 times/min
Inspection standard: 3.0mm thickness
(3)Drive Motor:
Uncoiler motor: 7.5KW * 1 unit
Leveling machine motor: 18.5KW * 1 unit (variable frequency speed regulation)
Servo feeding motor: 5.0KW * 1 unit (Estun)
Swing displacement motor: 11KW * 1 unit (Eston)
Hydraulic workstation motor: 3.75KW * 1 unit
1.Hydraulic Loading Trolley
Equipment Structure Description:
Style
Heavy duty frame welded with steel plate, oil-pressure & motor control
Quantity
1 set
V surface
Steel plate welded
Load-bearing
20 Tons
Lift stroke
350mm
Hydro-cylinder
Specification/Model:Φ125*350/HS6F
Power
2.2KW Geared Motor
Instructions:
a)The feeding trolley feeds horizontally to the parallel line of the uncoiler and rises vertically to align with the uncoiler
b) Main structure of the feeding trolley: composed of a lifting V-shaped platform and a movable base
c) It has parallel movement and vertical lifting, making it convenient to introduce the inner hole of the steel coil into the expansion and contraction tube of the unwinding machine
d) Horizontal movement power: The trolley's advance and retreat are driven by a deceleration motor; The lifting adopts hydraulic cylinder lifting
e)Hydraulic power: lifting weight ≤ 20 tons
f) The lifting stroke of the hydraulic cylinder is 350mm
g) Feed width: maximum 1250mm/minimum 200mm (minimum pillar required)
2.Single Head Cantilever Hydraulic Unwinding Machine:
Style
Heavy duty frame welded with steel plate, hydraulic expansion and contraction core shaft and gearbox structure
Quantity
1 Set
Load-bearing
20 Tons
Steel Coil Inner Dia
Ф480mm-Ф530mm-Ф610mm;
Steel Coil Outer Dia
Max: 1500mm
Tension Generation
Disc Brake Generates Tension
Material Release
Proactively Release
Open Power
AC7.5 KW Motor
Frequency Converter
7.5KW Frequency Converter
Motor
Domestic
Bearing
Domestic Havaro/UBC
Technical Parameter:
Instructions:
a) After aligning the steel coil with the center of the unwinding machine, the hydraulic feeding trolley automatically enters the steel coil into the unwinding machine, and the hydraulic pressure tightens the inner diameter. After the pressing arm is pressed down, the steel coil is released
b) Body structure: Adopting steel plate welded box body, double stack bearing seat, cantilever load-bearing coil material
c) The maximum load-bearing capacity of the body is ≤ 20 tons
d) The drum is composed of four sets of arc-shaped plates, and the oil cylinder pushes and pulls the main shaft to produce expansion and contraction
e) The range of the inner hole of the expandable and shrinkable coil material is from Ø 480mm to Ø 530mm to Ø 610mm
f) Active feeding 7.5KW cycloidal needle drive, variable frequency speed regulation
g) Functions include drum rotation, pneumatic brake, unwinding and pressure arm device, etc
3. Hydraulic Cantilever Supportor:
A)Purpose: To support the cantilever end of the unwinding machine drum and increase the rigidity of the drum rotation
B) The auxiliary support is an elbow rod mechanism, which is driven by a hydraulic cylinder to lift or lower the swing arm
C) When unwinding, the swing arm lifts to support the cantilever end of the unwinding machine, and when unwinding, the swing arm falls down
D) Body structure: using steel plate welded frame, support arm, oil cylinder, etc
4.Hydraulic Telescopic Material Plate:
A) Instructions for use: After the steel coil is untied, raise the receiving plate and extend the middle support plate to the steel coil head. Before entering the leveling machine, bend the head so that the steel coil head can smoothly enter the leveling machine;
B) Body structure: Adopting steel plate welded frame, guide rail sliding, hydraulic lifting, hydraulic power for bending material head roller;
C) The material receiving plate consists of an expansion plate, a material receiving plate, a material arc roller, an oil cylinder, etc.
5.Precision Board Leveling Machine:
Technical Parameters:
Style
Steel plate welded frame, motor drive, gear synchronization box
Quantity
1 Set
Structure
13 Roller leveling host machine
Fixed length mechanism
2-roll pinch feeding
Lift mechanism
Synchronous turbine lifting mechanism
Material of leveling roller
60CrMoV(≥HRC60)
Quantity of leveling roller
13-roll
Size of leveling roller
Φ130mm×1300mm
Working speed
5-20m/min
Feed roller diameter
Φ130mm
Number of feeding rollers
1 pairs
Drive motor
18.5KW
Frequency Converter
18.5KW Frequency Converter
Bearing
Domestic Havaro/UBC
Instructions:
A)After the board enters the leveling machine, the leveling machine is powered on and uses traction tension to unwind, and the unwinding machine is powered off. After passing through the leveling machine, the material does not loosen, the surface is not scratched, and the flatness is guaranteed. The running speed of the leveling machine is 18m/min
B)Structure: Single roll 13 roll leveling machine, 2-roll clamping, worm gear lifting
C)The leveling machine consists of a feeding traction roller, upper and lower leveling roller groups, a frame, an upper roller pressing and adjusting device, a transmission system, etc
D)Thirteen leveling rollers are arranged in a configuration of six in the upper part and seven in the lower part, with the lower row of leveling rollers installed on fixed supports and in the same working position
E)The upper leveling roller is installed on the movable slider (crossbeam) and its working position can be manually adjusted through the upper leveling roller pressing adjustment device. The upper leveling roller pressing device consists of a motor and a worm screw machine. By manually adjusting the working position of the slider on the feeding and discharging sides, the leveling gap and feeding and discharging angle between the upper and lower leveling rollers can be changed to adapt to different plate thicknesses. The upper and lower values are displayed on a digital display table
F)The traction roller is on the feeding side of the leveling machine, the upper and lower rollers are chrome plated with steel bars, and the worm screw is used for lifting and lowering
G)The traction down roller and all leveling rollers are driven by a variable frequency motor and reducer, through a gear distribution box and universal joint shaft, and the speed is automatically or manually adjusted by a variable frequency speed controller.
6.Material Pit Transition Bridge:
Instructions:
A)During the feeding process, there is no need for manual lifting and the steel coil can be smoothly fed into the feeder. The steel coil can be buffered by the material pit to ensure that the skewed feeder can freely move the steel strip left and right
B)Both ends of the transition bridge use hydraulic power to ascend and descend
C)The buffer bridge spans both ends of the pit, lifted during feeding and dropped during connecting operation, forming a loop of sheet metal in the pit
D)Two sets of photoelectric switches are installed at a certain depth in the pit, which control the speed conversion of the leveling machine and ensure that the boards hanging in the pit have sufficient length storage capacity
7. Anti Scratch Bracket at The Bottom of The Material Pit:
The material stop and start through induction during the working process, and the material arc contacts the bottom frame roller, effectively protecting the surface of the material from scratches and abrasions.
8.Side Guide Position Width Adjustment Device:
A) This machine guides the steel strip to enter the NC swing feeder correctly, and is connected to the swing feeder through steel plate welding
B) Both the feeding end and the discharging end adopt a four column guide wheel type, with two on each side, and the feeding width is adjusted by the handwheel screw
C) Material adjustment width: 50-1250mm
9. Left -Right Displacement Leveling Servo Feeder:
A) The device consists of two servo motor transmission systems, high-precision swing feeding, and material length detection device
B) Controlled by servo motors through human-machine interface and PLC, all parameter settings and operations are completed through touch screen control
C) There are 3 leveling rollers with a diameter of 130mm, with 1 upper roller and 2 lower rollers. The lower roller is fixed and the upper roller is adjustable. The rollers are driven by gears and synchronous wheels
D) There are a total of 4 feeding and sizing rollers with a diameter of 140mm, consisting of 2 upper rollers and 2 lower rollers. The lower roller is fixed, while the upper roller is adjustable,the rollers are driven by gears and synchronous wheels
E) Roller material: Made of 60CrMov material, the roller surface is treated with medium frequency HRC60-63 degree quenching and tempering, ground, and plated with hard chromium
F) Two linear guides (made of Taiwan silver, with a hardness of HRC 60~63C)
G) Two ball screws (made of Taiwan silver, with a hardness of HRC 60~63C)
H) Drive motor: 5.0KW/11KW servo motor driven by precision coupling and synchronous wheel
Main Configuration List:
No. |
Machine Region |
Name |
Specification/Power |
Brand |
1 |
Left-Right Swing & Displacement Feeder |
Feed Motor |
5.0KW |
ESTUN |
Deviation & Displacement Motor |
11KW |
ESTUN |
||
Transmission Gear |
6-Level Accuracy |
Fengheng |
||
Bearing |
Rolling Bearing |
UBC/DHW |
||
Linear Guide Rail |
|
HIWIN |
||
Ball Screw |
|
HIWIN |
||
Cabinet |
|
SHIXIANG |
||
2 |
Control System |
PLC Programmable Controller |
|
Siemens |
Touch Screen |
7” |
WEINVIEW |
||
Contactors, Relays, Circuit Breakers |
|
Schneider |