X-Ray Digital Imaging (DR) Detection System
X-Ray Nondestructive Testing for Circumferential & Longitudinal Welding of LPG Cylinders.
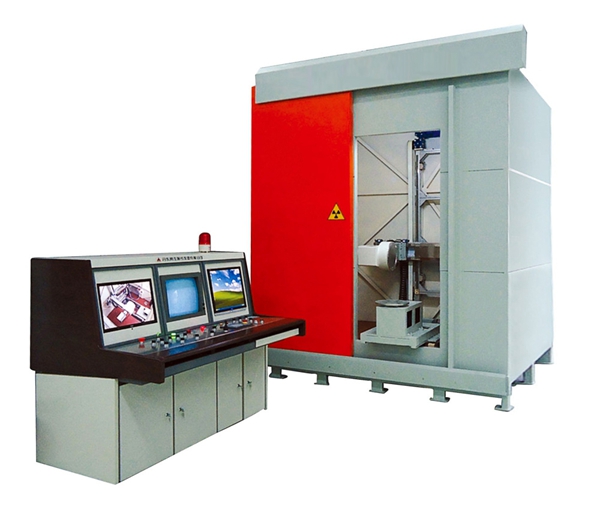
X-Ray Nondestructive Testing for Circumferential & Longitudinal Welding of LPG Cylinders.
This system is suitable for non-destructive testing in industries such as military, electronics, petroleum, chemical, refractory materials, steel pipes, die-casting, boilers, automobiles, pressure vessels, high-speed rail, aviation, aerospace, etc.
Realize dynamic real-time imaging, with fast operation speed and high image quality, improving detection speed and reliability. The system is equipped with a mechanical transmission device, which can be selected from different angles to observe internal defects and measure dimensions of the workpiece with excellent dynamic effects. Especially suitable for online testing.
Due to our company's outstanding contributions in this technology, it was designated by the National Development and Reform Commission as a high-tech industrialization base for the national X-ray real-time imaging detection system in 2004.
This product meets relevant national standards and has obtained a national radiation safety permit.
System composition
X-ray inspection machine
Imaging unit
Detection platform
Image processing unit
Lead protection system
Imaging method optional
X-ray digital flat panel detector
High resolution micron level linear array digital detector
Mechanical inspection and scanning platform
Basic type: Four axis motion detection scanning method
Standard type: Five axis motion detection scanning method
Functional type: multi axis motion detection scanning method
Main parameters of the system
System resolution: 16Lp/cm-40Lp/cm, 50Lp/cm-60Lp/cm
System sensitivity: 0.7%-2%
Tube voltage: 20kV-450kV
Tube current: 0mA-20mA
Main functions of image processing software
Optimization of electronic filming and image storage
Window, window level technology, multiple smooth noise reduction options
2-512 image denoising, improving image resolution and sensitivity
Edge enhancement, sharpening, negative image, pseudo color, real-time scaling
Measurement of defect size and grayscale level
Printing reports that can record workpiece codes, inspection dates, operators, defect types, etc
Laser positioning
Dynamic storage and playback
Equipped with applicable application software that can achieve automatic recognition function
Equipped with automatic control of detection system and automatic control of image defects
X-ray non-destructive testing, as an important means of testing the quality of castings, can most intuitively reflect the size, shape, type, and distribution of internal defects in castings. The standards released this time stipulate the grading and compensation rules, general requirements, detection techniques, image evaluation, detection records and reports for X-ray digital imaging detection technology using digital detector arrays (DDA) for castings. Suitable for castings and other metal material castings produced using various casting techniques.
The Aolong Ray Group, which has inherited more than 50 years of history in the development of X-ray instruments in China, has been committed to the research and application of X-ray in the casting field for a long time. It has broken traditional thinking and innovatively launched various detection methods, gradually promoting the development of digital X-ray imaging detection technology for castings towards online, intelligent, and automated detection. It provides more accurate, efficient, and diverse detection solutions for the casting industry, and shoulders the mission and responsibility of China's X-ray base.
Model: XYG-22508/3
X-Ray Nondestructive Testing for Circumferential & Longitudinal Welding of LPG Cylinders
Applicable Workpieces Specification:
1. Materials of LPG cylinder: S30408、06Cr19Ni10 、SUS304 and others
2. Diameter range of LPG cylinders: φ300mm~φ650mm
3. Length range of LPG cylinders: 800mm~1500mm
4. Single wall thickness range of LPG cylinders: 2mm~5mm(not including the collar and footring)
5. The Max.weight of LPG cylinder: ≤500kgs
6. Application: Testing circumferential and longitudinal welding of LPG cylinders
Description:
1. The flaw detection technical indicators meet the AB level requirements of the JB/T4730 standard in image processing testing
2. The system resolution shall not be less than 2.5 LP/mm (tested on image processing in accordance with JB/T10815 "Non-destructive Testing - Test Target for Image Resolution in Radiographic Testing")
3. The movement mode of the detection tooling meets the requirements for non-destructive testing of internal circumferential and longitudinal welds. During X-ray digital imaging testing of a single weld on a single gas cylinder, the positioning is accurate
4. Party B shall recommend the brand, model, and other parameters of the image quality indicator (IQI). The sensitivity of the recommended IQI must comply with the AB level requirements specified in the JB/T4730.2 standard
5. The resolution within the effective evaluation area of the image shall not be less than 2.5 LP/mm (tested in accordance with JB/T10815 "Non-destructive Testing - Test Target for Image Resolution in Radiographic Testing")
6. The system software includes defect marking (allowing direct insertion of representative symbols or text, such as pores, lack of fusion, etc.), defect size measurement and calibration functions; it also provides browsing and searching capabilities for images and related information within the images; it includes image processing functions such as window selection, noise reduction, brightness and contrast enhancement; and it saves the noise-reduced image data as original image data
7. Images are stored in the standard DICONDE format. Information such as workpiece number, weld number, penetrated thickness, radiographic parameters, geometric dimension calibration results, and defect interpretation markings can be written into the image description field of the image file. This information shall be unalterable. Each inspection image file can be annotated with necessary information identifiers such as workpiece number, weld number (A-longitudinal weld, B1-circumferential weld, B2-circumferential weld), and inspection date. These identifiers are directly written into the image file during storage and cannot be altered
8. The power supply in the X-ray testing room uses a dedicated ground wire with a resistance of less than 3 ohms
9. Gas cylinder production is carried out in batches. Each gas cylinder shall have a unique identification number for traceability. If there are multiple inspection images for any weld on a gas cylinder, the numbering shall be continuous and unique, automatically incremented by the system software. If a weld requires rework, the reworked weld on the gas cylinder shall have a unique number that is correlated and identifiable with the original number (manually entered)
10. The image distortion rate complies with the standard
Compliant Standards
1. The entire system complies with GB/T 17925-2011 "X-ray Digital Imaging Inspection of Butt Welds in Gas Cylinders."
2. The X-ray machine system complies with JB/T 7412 "Stationary (Mobile) Industrial X-ray Inspection Equipment."
3. Image Quality:
JB/T 4730 "Non-destructive Testing of Pressure Equipment"
JB/T 7902 "Non-destructive Testing - Wire-type Image Quality Indicators"
JB/T 10815 "Non-destructive Testing - Test Target for Image Resolution in Radiographic Testing"
JB/T 5453 "Technical Specifications for Industrial X-ray Image Intensifier Television Systems"
4. Lead Protection Room: GBZ 117-2006 "Radiological Protection Standards for Industrial X-ray Inspection"
System Composition and Technical Parameters
The system mainly consists of seven parts: a stationary X-ray inspection machine, an imaging system, a computer image processing system, a protection system, an electrical control system, a mechanical system, and an on-site monitoring system.
1. System Resolution: Not less than 2.5 LP/mm (tested after image processing).
2. Inspection Speed (Linear Speed): 0~3 m/min, stepless speed regulation. The operator adjusts the speed using the speed control knob on the operation panel.
3. System Sensitivity:
Dynamic Sensitivity: 2.2~3.0% (at speed ≤ 2.5 m/min)
Static Sensitivity: 1.5~2.0% (after image processing)
4. The system can operate in two modes: X-ray electronic radiography and real-time imaging display.
5. All painted parts must comply with the color requirements specified by the buyer (the buyer provides the color card)
Composition and Technical Parameters of System Components
I. Technical Parameters of the X-ray Machine System
Tube Voltage Adjustment Range: 40~225 kV, continuously adjustable
Step Size: 1 kV
Accuracy: ±1%
Tube Current Adjustment Range:
0~8 mA (large focus), continuously adjustable
0~3.5 mA (small focus), continuously adjustable
Step Size: 0.1 mA
Accuracy: ±1%
Focus Size: Complies with EN12543 standard
d = 0.4 mm (small focus)
d = 1.0 mm (large focus)
Cooling Method:
Anode forced circulating water cooling
Minimum Water Flow Rate: 4 L/min
Maximum Penetration Capability (Stainless Steel): ≤20 mm (under real-time imaging conditions, focal distance of 600 mm)
Power Supply Requirements:
1. Grid Frequency: 50Hz ± 1%
2. Voltage: 380/220V ± 10%, three-phase five-wire system, independent power supply.
3. Single-Phase Capacity: Not less than 5 kVA, independent and pollution-free power supply.
4. Grid Fluctuation: Should not exceed ±5% of the rated voltage.
5. Grounding: Independent grounding wire (resistance < 3 ohms), equipped with leakage protection and voltage stabilization devices (to be provided by the buyer).
Compressed Air Pressure:
Not less than 0.6 MPa.
Control Room Requirements:
The buyer should equip the control room with air conditioning.
Additional Requirements:
For foundation preparation, power/gas supply requirements, and site conditions that require the buyer's cooperation, the supplier will provide formal and detailed documentation to the buyer within two weeks after the contract is signed.