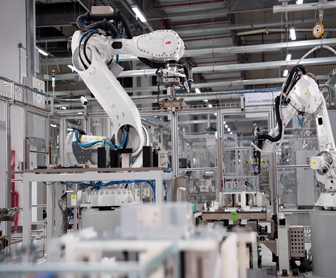
Composite LPG Cylinder Production Line Process:
1.Blow Molding For HDPE Inner Liner
2.Cooling
3.Valve Seat Welding & Testing
4.Liner Surface Treatment
5.Winding
6.Curing
7.Air Tightness/Water Pressure Test
8.Valve Installation
9.Injection Molding of Outer Protective Casing
10.Air Pressure Supply
11.Central Control System
HDPE inner liner integral winding resin impregnated long fiber reinforcement composite LPG cylinder technology:
Fiber wound composite gas cylinders are generally composed of inner lining, fibers, resins, etc. The inner wall of the composite gas cylinder inner lining is directly in contact with the medium, and its main functions are airtightness, anti-corrosion, temperature resistance, and pressure resistance; Therefore, it is required that the lining material have good airtightness, corrosion resistance, temperature resistance, high strength, and high toughness There are two commonly used lining materials: aluminum and plastic The main function of fiber winding reinforced composite material layer is to ensure that the gas cylinder has sufficient strength, stiffness, and stability under stress The composite material winding layer bears the vast majority (75%~95%) of the pressure load, with fibers as the main load-bearing body, and resin plays a bonding role on the fibers, distributing and transmitting loads between them; Therefore, selecting high-strength and highly elastic reinforcing fibers and high-performance resins is an important measure to improve the load-bearing capacity of structures High performance composites such as high-strength glass fiber epoxy resin or carbon fiber epoxy resin and Kevlar fiber epoxy resin are usually used.
Composite material gas cylinders are generally classified into two methods: firstly, according to the application field, they are divided into: 1. Fuel gas cylinders for natural gas, hydrogen, and other fuel vehicles; 2. Used for respirator systems, including backpack mounted respirators, small respirators, and breathing masks for escape; 3. Used for aviation or navigation, mainly including escape slide inflation devices and aviation oxygen absorption devices; 4. Liquefied gas cylinders for household use, etc.
Classification by liner material and reinforcement material: According to liner material, it can be divided into metal liner wrapped gas cylinders and plastic liner wrapped gas cylinders; It can also be divided into high-strength glass fiber wound gas cylinders, carbon fiber wound gas cylinders, aramid fiber wound gas cylinders, etc. according to the reinforcing materials Due to the advantages of good sealing, strong fatigue resistance, long cycle life, high stability, and light weight, aluminum liners are currently widely used in carbon fiber wound gas cylinders.
Fiber wound composite gas cylinders have the following advantages: 1. Light weight, good rigidity, and high strength; 2. The fatigue failure of metal materials is usually a sudden failure without obvious omen, and the combination of reinforcement and matrix in composite materials can not only effectively transfer the load, but also prevent the crack growth, which improves the fracture toughness of gas cylinders; 3. When a large number of reinforced fibers in composite materials cause material overload and a few fibers break, the load will be quickly redistributed to the undamaged fibers, so that the entire gas cylinder will not lose its load-bearing capacity in a short period of time; 4. Composite gas cylinders will not produce dangerous fragments when damaged by impact or high-speed impact, thereby reducing or avoiding injury to personnel; 5. It can meet the requirements of corrosion resistance without special treatment.
For more information, please refer to the next product.
Fully automated production
Cost effective and highly automated manufacturing process
All manufacturing process are fully automated the LPG cylinder is built from raw materials to finished product1.Blow-Molder
2.Robot
3.Inspection Table
4.Injection Molding Machines
5.Corona/Flame Treatment
6.Spin Welding
7.Resin Feeder
8.Filament Winding Machines
9.Ovens
10.Test Equipment
11.Injection Molding Machines
12.Conveyer Belt
13.Injection Molding Machines
14.Packing,Sub-Assembly
Frequency transformer,Valve,Servo pump,Pneumatic valve,Electronic components,Screw Motor,Bearing,Oil seal,Electronic control system,Gearbox,Air cylinder,all parts and components come from top brand:
Automatic composite cylinder production line
Model: PBI-905X
Single station
Storage type single die head
Single layer
Storage capacity: 5kg
Matching the raw materials of the machine: (Marlex)HDPE or equivalent
Electronic control system: BECKHOFF Germany
Specifications of finished inner liner: 36L 47L
Net weight of finished inner liner: 1.35kg 1.6kg
Molding cycle time: 90±2S,the final cycle is based on the product provided by the customer
Automatic sealing machine 1 set
Automatic overflow removal device 1 set
Thickness control system 100 point,valve MOOG Japan 1 set
Three point combination (automatic periodic filtration of moisture) 1 set
Cooling fixture and fixture device 1 set
Bottom overflow conveyor line (one straight line) 1 set
36L mold (including auxiliary mold) material: 7075 aluminum+cut beryllium copper inlay 1 set
47L mold (including auxiliary mold) material: 7075 aluminum+cut beryllium copper inlay 1 set
General specification:
A、The annual output of this production line is 300,000 pieces,it runs 20 hours a day
B、Total electric power 600KW
C、Production area 2000 ㎡(Storage space excluded)
D、Plant height ≥ 7M,equipment inlet width ≥5M,equipment entry height ≥ 5M