LPG Cylinder Shot Blasting Machine
This shot blasting machine uses the world's advanced single disc linear blade high-efficiency shot blaster to shoot high-speed and dense bullet beams, striking various parts of the original state steel for three-dimensional and all-round cleaning, causing the rust layer, welding scar, oxide skin and dirt on the surface of the steel to quickly fall off, obtaining a smooth surface with a certain roughness, and improving the adhesion between the paint film and the steel surface, And it improves the fatigue strength and corrosion resistance of the steel, improves the internal quality of the steel, and extends its service life.
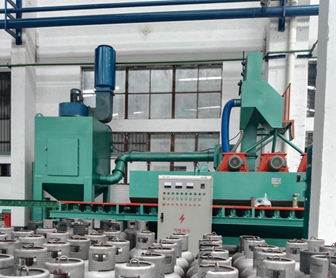
Main Technical Parameters:
Shot blasting machine main part
1. Shot blasting machine
(1) The projectile ejection speed is 95-100 m/s
(2) Bullet flow rate 220kg/min
(3) Power 2 * 7.5kw
2. Processing efficiency: ≥ 135m2/h
3. Handle cylinder diameter: φ 219-406mm
4. Cleaning requirements: comply with GB8923-88 A-B Sa2 1/2 standard
5. Production rhythm: On average, about 1 piece per minute
6. Using pellets: steel pellets or steel wire cut pellets Φ 1.0 to 1.5
7. Roller conveyor speed: 1-4r/min
8. Bucket elevator: lifting capacity: 45t/h, power: 4 kW
9. Spiral conveyor: conveying capacity: 45t/h, power: 2.2 kW
10. Separators: Separation capacity: 45t/h, separation zone wind speed: 4-5 m/s
11. Equipment noise: ≤ 90 dB
Dust removal and desulfurization system part
1.Processing air volume: not less than 3000m3/h
2.Total filtration area: not less than 57m2
3.Dust concentration at the inlet: ≤ 1200mg/Nm3
4.Export dust concentration: ≤ 50mg/Nm3
Equipment Configuration:
1.One upcast gas cylinder rust removal machine
2.Dust removal system: 1 set
3.Desulfurization system: 1 set
3.2 bottle racks for entry and exit
4.Electrical control system: 1 set
5.High pressure fan: 1 unit
Shot blasting machine main part
1. Shot blasting machine
(1) The projectile ejection speed is 95-100 m/s
(2) Bullet flow rate 220kg/min
(3) Power 2 * 7.5kw
2. Processing efficiency: ≥ 135m2/h
3. Handle cylinder diameter: φ 219-406mm
4. Cleaning requirements: comply with GB8923-88 A-B Sa2 1/2 standard
5. Production rhythm: On average, about 1 piece per minute
6. Using pellets: steel pellets or steel wire cut pellets Φ 1.0 to 1.5
7. Roller conveyor speed: 1-4r/min
8. Bucket elevator: lifting capacity: 45t/h, power: 4 kW
9. Spiral conveyor: conveying capacity: 45t/h, power: 2.2 kW
10. Separators: Separation capacity: 45t/h, separation zone wind speed: 4-5 m/s
11. Equipment noise: ≤ 90 dB
Dust removal and desulfurization system part
1.Processing air volume: not less than 3000m3/h
2.Total filtration area: not less than 57m2
3.Dust concentration at the inlet: ≤ 1200mg/Nm3
4.Export dust concentration: ≤ 50mg/Nm3
Equipment Configuration:
1.One upcast gas cylinder rust removal machine
2.Dust removal system: 1 set
3.Desulfurization system: 1 set
3.2 bottle racks for entry and exit
4.Electrical control system: 1 set
5.High pressure fan: 1 unit
Product Image for Reference:
Features:
This equipment is a roller conveyor high-performance shot blasting cleaning equipment. During the cleaning process, the cycloidal pinwheel reducer drives the conveyor roller to send the steel cylinder into the cleaning room's ejection area, and the steel cylinder rotates simultaneously. In the ejection zone, the steel cylinder is hit and rubbed by dense and powerful projectiles from the two upper shot blasting assemblies. The oxide skin and dirt on it quickly fall off, and the steel surface obtains a bright surface with a certain roughness. At the same time, the workpiece is relieved of stress and deformed due to the dense and strong impact. During the cleaning process, the scattered shot dust mixture is collected in the lower shell of the elevator through the chamber feeding screw conveyor, and then reaches the separator through the elevator and conveyor. After passing through the separator, a shot dust waterfall is generated, which is blown by the air outlet to remove the dust. The separated clean shot falls into the separator
The separator hopper is ejected by the shot blaster through the shot conveying system. The air dust from the separator and cleaning room is driven by a ventilation fan, and is removed by a pulse dust collector through an air duct pipeline system, with an efficiency of up to 99%. After purification, the air is discharged into the atmosphere through a chimney, and particulate dust is captured and collected.
This equipment consists of the following functional parts: main and auxiliary cleaning rooms, shot blasting assembly, conveying system, shot chute, elevator, separator, shot conveying system, dust removal system, electrical control system, etc.
1. Cleaning room
(1) Structure
This cleaning room consists of the main and auxiliary cleaning rooms, which are large capacity chamber structures. The upper part of the chamber is box shaped, and the lower part is conical. The cleaning operation is carried out in a sealed chamber, including the front and rear auxiliary chambers, the main chamber, rubber curtains, shot blasting chamber guards, shot blasters, etc.
A. There are two shot blasters installed on the main chamber, and the spatial structure has been tested and verified to achieve optimal cleaning of the workpiece.
B. The cleaning room is a multi chamber combination, with sealed chambers in both the front and back, and multiple layers of rubber curtains inside to prevent bullets from flying out. At the same time, there is a certain negative pressure inside to prevent dust from escaping.
C.Wear resistant protective plates are installed inside the main chamber to protect the wall panels from wear and prolong the service life of the chamber by tens of times. At the same time, the reflection function of the projectile can be utilized to continue to effectively hit the surface of the workpiece, improving cleaning quality and efficiency. Mesh and pedals are installed on both sides of the conical shot collecting hopper to block debris and protect the screw conveyor, making it easy for maintenance personnel to walk.
D. The protective plate inside the shot blasting chamber is covered and bolted with wear-resistant nuts to protect the bolt head from damage and facilitate disassembly and replacement.
(2) Adjusting usage and maintenance safety
A. The protective plate and cast nut inside the shot blasting room are vulnerable parts that must be regularly checked for wear and replaced in a timely manner. When installing the protective plate, attention should be paid to overlapping to prevent damage to the wall panel and endangering safety.
B. Cleaning indoor rubber curtains is a vulnerable part. If there is any damage, it should be repaired and replaced in a timely manner to prevent bullets and dust from escaping.
C. During work, personnel should stay away from the entrance and exit of the room to prevent projectiles from splashing into the eyes, and a warning sign should be hung.
D.When entering the cleaning room for maintenance, it is necessary to cut off the power supply in advance, hang a warning sign, and strictly prohibit electric operation. Violators may endanger personal safety.
This equipment is a roller conveyor high-performance shot blasting cleaning equipment. During the cleaning process, the cycloidal pinwheel reducer drives the conveyor roller to send the steel cylinder into the cleaning room's ejection area, and the steel cylinder rotates simultaneously. In the ejection zone, the steel cylinder is hit and rubbed by dense and powerful projectiles from the two upper shot blasting assemblies. The oxide skin and dirt on it quickly fall off, and the steel surface obtains a bright surface with a certain roughness. At the same time, the workpiece is relieved of stress and deformed due to the dense and strong impact. During the cleaning process, the scattered shot dust mixture is collected in the lower shell of the elevator through the chamber feeding screw conveyor, and then reaches the separator through the elevator and conveyor. After passing through the separator, a shot dust waterfall is generated, which is blown by the air outlet to remove the dust. The separated clean shot falls into the separator
The separator hopper is ejected by the shot blaster through the shot conveying system. The air dust from the separator and cleaning room is driven by a ventilation fan, and is removed by a pulse dust collector through an air duct pipeline system, with an efficiency of up to 99%. After purification, the air is discharged into the atmosphere through a chimney, and particulate dust is captured and collected.
This equipment consists of the following functional parts: main and auxiliary cleaning rooms, shot blasting assembly, conveying system, shot chute, elevator, separator, shot conveying system, dust removal system, electrical control system, etc.
1. Cleaning room
(1) Structure
This cleaning room consists of the main and auxiliary cleaning rooms, which are large capacity chamber structures. The upper part of the chamber is box shaped, and the lower part is conical. The cleaning operation is carried out in a sealed chamber, including the front and rear auxiliary chambers, the main chamber, rubber curtains, shot blasting chamber guards, shot blasters, etc.
A. There are two shot blasters installed on the main chamber, and the spatial structure has been tested and verified to achieve optimal cleaning of the workpiece.
B. The cleaning room is a multi chamber combination, with sealed chambers in both the front and back, and multiple layers of rubber curtains inside to prevent bullets from flying out. At the same time, there is a certain negative pressure inside to prevent dust from escaping.
C.Wear resistant protective plates are installed inside the main chamber to protect the wall panels from wear and prolong the service life of the chamber by tens of times. At the same time, the reflection function of the projectile can be utilized to continue to effectively hit the surface of the workpiece, improving cleaning quality and efficiency. Mesh and pedals are installed on both sides of the conical shot collecting hopper to block debris and protect the screw conveyor, making it easy for maintenance personnel to walk.
D. The protective plate inside the shot blasting chamber is covered and bolted with wear-resistant nuts to protect the bolt head from damage and facilitate disassembly and replacement.
(2) Adjusting usage and maintenance safety
A. The protective plate and cast nut inside the shot blasting room are vulnerable parts that must be regularly checked for wear and replaced in a timely manner. When installing the protective plate, attention should be paid to overlapping to prevent damage to the wall panel and endangering safety.
B. Cleaning indoor rubber curtains is a vulnerable part. If there is any damage, it should be repaired and replaced in a timely manner to prevent bullets and dust from escaping.
C. During work, personnel should stay away from the entrance and exit of the room to prevent projectiles from splashing into the eyes, and a warning sign should be hung.
D.When entering the cleaning room for maintenance, it is necessary to cut off the power supply in advance, hang a warning sign, and strictly prohibit electric operation. Violators may endanger personal safety.
Shot Blasting Machine Specification:
(1) The projectile ejection speed is 95-100 m/s
(2) Bullet flow rate 220kg/min
(3) Power 2 * 7.5kw
2. Processing efficiency: ≥ 135m2/h
3. Handle cylinder diameter: φ 219-406mm
4. Cleaning requirements: comply with GB8923-88 A-B Sa2 1/2 standard
5. Production rhythm: On average, about 1 piece per minute
6. Using pellets: steel pellets or steel wire cut pellets Φ 1.0 to 1.5
7. Roller conveyor speed: 1-4r/min
8. Bucket elevator: lifting capacity: 45t/h, power: 4 kW
9. Spiral conveyor: conveying capacity: 45t/h, power: 2.2 kW
10. Separators: Separation capacity: 45t/h, separation zone wind speed: 4-5 m/s
11. Equipment noise: ≤ 90 dB
(1) The projectile ejection speed is 95-100 m/s
(2) Bullet flow rate 220kg/min
(3) Power 2 * 7.5kw
2. Processing efficiency: ≥ 135m2/h
3. Handle cylinder diameter: φ 219-406mm
4. Cleaning requirements: comply with GB8923-88 A-B Sa2 1/2 standard
5. Production rhythm: On average, about 1 piece per minute
6. Using pellets: steel pellets or steel wire cut pellets Φ 1.0 to 1.5
7. Roller conveyor speed: 1-4r/min
8. Bucket elevator: lifting capacity: 45t/h, power: 4 kW
9. Spiral conveyor: conveying capacity: 45t/h, power: 2.2 kW
10. Separators: Separation capacity: 45t/h, separation zone wind speed: 4-5 m/s
11. Equipment noise: ≤ 90 dB
As per country standard